제어 캐비닛 구축의 디지털화를 위한 미래 기회
종이를 쓰지 않는 생산으로의 여정
시리즈 생산과 일회성 생산을 막론하고 기존 제어 캐비닛 구축에는 많은 수작업 단계가 수반되어 공정에 시간과 비용이 많이 듭니다. 이러한 가운데 전체 가치 사슬에 걸친 엔드-투-엔드 디지털화는 유연성, 투명성과 더불어 생산성 증대를 보장하는 솔루션입니다. 완전히 디지털화된 공정 흐름은 생산 및 계획의 효율성을 40% 가까이 향상시킵니다.
제어 캐비닛 구축의 목표는 다양한 공정을 상호 연결하고 모든 작업 단계에서 생성되는 데이터를 중앙에서 관리하는 것입니다. 새로운 데이터가 다른 시스템에 입력될 때나 회로도가 종이 형식으로 발행될 때 발생할 수 있는 미디어 중단을 방지하는 것도 목표 중 하나입니다. 공정 연결성은 효율성을 상당 부분 향상시켜 제조업자에게 혜택을 가져다줄 수 있습니다. 예를 들어, CAD 시스템에서의 전기 설계와 레이아웃 계획 등의 개별 작업 단계를 기계 생산, 배선 및 최종 테스트로 연결하면, 부품 리스트 데이터를 수동으로 옮기는 등의 노력을 최소화할 수 있습니다. 또한, 이미 설계 부서에서 사용하고 있는 정보를 여러 번 수동으로 입력하는 작업도 방지할 수 있습니다. 이러한 수동 작업은 작업 시간을 늘릴 뿐만 아니라 오류의 가능성 역시 높입니다. 개별 공정 단계가 상호 연결되지 않는다면, 원래 주문에 변경이 발생할 경우 여러 시스템에 이러한 변경 내역을 반영해야 합니다.
전망과 현 상황: 제어 캐비닛 구축에서의 디지털 트윈
디지털 트윈은 제어 캐비닛 구축에 필요한 여러 작업 단계를 연결하는 데 많은 이점을 제공할 수 있습니다. 트윈은 전기 설계와 레이아웃 계획 단계에서 생성되며, 전체 생산 단계에서 각 부서에 필요한 정보를 제공하게 됩니다. 디지털 트윈이 특별한 이유는 고객과 제조업체, 공급업체가 동일한 모델로 작업할 수 있기 때문입니다. “Siemens, Schneider 또는 SEW와 같은 디바이스 제조업체들은 자사 제품의 모든 속성이 포함된 EPLAN 매크로를 제공하고 있습니다. 우리 전기 설계자들은 이러한 장치를 회로도에 삽입해 회로 버전의 모델을 생성합니다.” Unitechnik Systems GmbH의 제어 캐비닛 구축 생산 매니저인 Mathias Terstegen은 설명합니다. 레이아웃 플래너는 가상 인클로저에 장치를 위치시키고, 모델을 물리적인 형태로 만들게 됩니다. 완성된 모델에는 모든 차원이 포함되며, 현실적인 3D 형태로 개별 장치의 내부를 살펴볼 수 있습니다. 또한 모든 케이블 라우팅이 포함된 완벽한 배선과 덕트, DIN 레일(위치 및 길이)과 모든 컷아웃 및 드릴 구멍 등도 포함됩니다. 햅틱 묘사는 각기 다른 기술 분야에 해당하는 작업을 쉽게 식별하기 때문에 작업의 상당 부분을 단순화합니다. 그렇기 때문에 생산 시간이 단축되며, 오류가 발생할 가능성도 대폭 감소합니다.
기계 제조의 자동화
트윈에 저장된 데이터는 다른 이점도 제공합니다. 바로 케이블 덕트와 DIN 레일 길이가 자동으로 생성된다는 것입니다. 각 캐비닛에 자재 정보를 제공하는 자동 케이블 덕트와 DIN 레일 절단기 덕분에 측정과 수동 절단을 할 필요가 없습니다. 또한 디지털 트윈이 제공하는 정밀 데이터는 다른 공정 단계에도 높은 가치를 제공합니다. “드릴링과 밀링 기계는 드릴 구멍과 컷아웃의 정확한 위치를 알아내기 위해 3D 모델이 제공하는 데이터를 활용합니다.” Terstegen은 말합니다. 자동화된 플로팅과 프린팅 스테이션은 개별 부품 라벨링에 들어가는 수고도 줄여줍니다. 터미널 스트립 생산을 아웃소싱해 공정 디지털화로 효율성을 증진한 사례도 있습니다. 디지털 트윈을 통해 완성 터미널 스트립을 서비스 공급업체에게 보내기만 하면 공급업체는 완전히 라벨링되고 구성된 터미널 스트립을 주문할 수 있으며, 서비스 제공업체는 이를 완전 자동으로 제조합니다. “이러한 기계는 대량건이 지속적으로 있어야만 투자금을 회수할 수 있습니다.” Terstegen은 말합니다. “따라서 제조업체는 어떤 기계에 투자를 하고 무엇을 아웃소싱할지 합리적으로 결정해야 합니다.” 케이블 역시 조건에 따라 미리 조립할 수 있습니다.
스마트한 배선으로 가능해진 종이 없는 생산
스마트한 배선으로 종이 없는 생산에 한 단계 더 다가갑니다. 시스템 전체 배선을 디지털 트윈으로 시각화할 수 있기 때문입니다. 배선을 위해 인쇄된 회로도는 과거의 유물이 되고, 태블릿으로 직접 3D 모델을 보며 작업할 수 있게 되는 것입니다. 디지털 트윈은 케이블 길이와 케이블 라우팅, 터미널 지점을 확인하기 위해 사용됩니다. 이러한 시스템은 케이블 덕트가 일정한 충전 용량을 가지고 있는지 확인합니다. 디지털 트윈은 여러 부서가 동일한 모델을 동시에 작업할 때 실시간으로 현재 공정 상태를 확인할 수 있게 해줍니다. 따라서 작업에 임하는 당사자들을 위해 변경 내역들이 항상 투명하고 정확하게 문서화됩니다. “우리에게 중요한 것은 공정을 디지털화하여 변경 내역들을 유연하게 통합할 수 있느냐 하는 것이었습니다.” Terstegen는 말합니다. 수정 내역이 발생하면 전기 설계자들은 수정된 부품의 배전이 이미 완료되었는지 온라인에서 확인할 수 있고, 변경 내역은 배전 기술자의 태블릿에 즉시 나타나게 됩니다. 반대로 배전 기술자가 오류를 찾아낼 수도 있습니다. 그러면 변경 내역이 전기 설계자에게 실시간으로 전송됩니다.
스위치기어 엔지니어링에서의 인터페이스 문제
전사 차원에서 데이터를 전송할 때의 문제는 제어 캐비닛 3D 모델을 위한 표준화된 인터페이스가 없다는 것입니다. 건물 부문 등 다른 산업군에서는 IFC 인터페이스가 건물의 3D 표현을 표준화합니다. 하지만 엔지니어링에서도 이제 EPLAN Pro Panel을 통해 제어 캐비닛의 디지털 트윈을 3D로 표현할 수 있습니다. 3D 모델을 기반으로 다운스트림 공정에서 필요로 하는 모든 정보가 표준화된 인터페이스를 통해 제공될 수 있습니다. 고객과 서비스 공급업체도 자사의 공정을 위해 디지털 트윈이 제공하는 데이터를 활용할 수 있습니다. 정보를 공유하기 위한 추가 문서가 전혀 필요 없다는 것입니다.
전사 차원의 유연성
디지털 트윈으로 작업한다는 것은 모든 관계자가 최신 정보를 받아본다는 뜻입니다. 때문에 전사 차원에서, 고객과 캐비닛 제조업체 사이에서, 그리고 캐비닛 제조업체와 공급업체 사이에서 고도로 효율적인 협업이 가능해 집니다. 고객 역시 공정와 프로젝트 진행 상황에 대한 개요를 한눈에 확인할 수 있습니다. 아주 사소한 디테일까지도 바로 확인이 가능합니다. 문제가 발생할 경우 모델을 함께 확인하고 논의할 수 있기 때문에 문제 해결이 수월해 집니다.
Unitechnik 소개
Unitechnik Systems GmbH는 Wiehl에 기반을 두고 있는 기업으로서, 40년이라는 세월 동안 산업용 자동화 및 정보 기술 분야 최고의 공급업체 자리를 지키고 있습니다. 가족 중심으로 운영되는 해당 기업의 2세대는 내부 물류와 화물 시설 및 생산을 위한 맞춤화된 시스템을 설계 및 실행하고 있습니다. Unitechnik는 시스템 통합 기업이자 종합 공급업체로서 전 세계에서 비즈니스를 운영하고 있습니다. 전문적인 프로젝트 관리와 플랜트 실행 지원은 장기 비즈니스 관계의 기반이며, 고객 투자의 안정성을 보장합니다. Unitechnik 고객에는 Claas, Dehn, Emirates, Linde, Lindt & Sprüngli, Nobilia, Otto Fuchs, Soennecken 및 Turck 등 유명 기업들이 포함됩니다.
저자: Unitechnik 제어 캐비닛 엔지니어링 부문 및 영업 책임자 Dirk Schütz
Conventional control cabinet construction, both for series and one-off production, involves many manual work steps making the process both time-consuming and costly. End-to-end digitalisation along the entire value chain is however a solution that promises to increase productivity along with flexibility and transparency. Fully digitalised process flows increase efficiency in production and planning by almost 40 percent.
The goal in control cabinet construction is to connect the various processes with each other and to centrally manage the resulting data for all work steps. To be avoided are media breaks, such as those that occur when new data is entered into other systems or when schematics are issued in paper format. Connected processes mean manufacturers benefit from significantly more efficient processes. Connecting individual work steps such as electrical design in the CAD system and layout planning through to mechanical production, wiring and final testing minimises any effort required for tasks such as the manual transfer of parts list data. Other tasks that can be avoided include multiple manual input of information that is already available from the design department. Such manual tasks not only tie up working time, but also increase the likelihood of errors. When individual process steps are not connected with each other, any changes made to the original order then require implementation in multiple systems.
Outlook and status quo: The digital twin in control cabinet construction
Digital twins significantly increase the benefits in connecting the work steps in control cabinet construction. The twin is created during electrical design and layout planning and then accompanies the entire production process providing the individual departments with the necessary information. What makes a digital twin special is that customers, manufacturers and suppliers all work with the same model. "Device manufacturers such as Siemens, Schneider or SEW, provide EPLAN macros which include all the properties of their products. Our electrical designers insert these devices into their schematics and thus generate a logical version of the model", explains Mathias Terstegen, production manager for control cabinet construction at Unitechnik Systems GmbH. The layout planner then puts the model into a physical form by placing the devices in the virtual enclosure. The finished model includes all dimensions and portrays the individual devices inside in a realistic 3D look. Also included is the complete wiring with all cable routing, ducts and DIN rails (positions and lengths) as well as all holes and cut-outs. The haptic portrayal simplifies much of the work as tasks for the different technical disciplines are easy to identify. Production is then less time-consuming and the likelihood of errors decreases significantly.
Automation of mechanical manufacturing
The data stored in the twin also brings further benefits. Cable duct and DIN rail lengths are generated automatically. Measuring and manual cutting are no longer necessary with an automatic cable duct and DIN rail cutter providing the material for each cabinet. The precision data from the digital twin also delivers high value for other process steps. "Drilling and milling machines get their data from the 3D model for the precise position of drill holes and cut-outs", says Terstegen. Automated plotting and printing stations additionally save personnel the effort of labelling the individual components. Outsourcing terminal strip production is a further example of increased efficiency through digitalised processes. Fully labelled and configured terminal strips can be ordered from suppliers by sending the finished terminal strip from the digital twin to the service provider, who then manufactures it fully automatically. "Such a machine can pay for itself only when large quantities are continuously required", says Terstegen. "Manufacturing companies can therefore decide which machines makes sense to invest in and what can be outsourced". Cables can also be pre-assembled according to requirements.
Paperless production thanks to smart wiring
Smart wiring represents a further step towards paperless production. It enables the entire wiring of the system to be visualised via a digital twin. Printed schematics for the wiring then become a thing of the past with the work instead being done via tablet directly on the 3D model. The digital twin can be used to read out cable lengths, cable routing and terminal points. The system ensures the cable ducts have consistent fill capacities. The digital twin also enables the current processing status to be seen in real time when several departments are working simultaneously on the model. Changes are thus transparent and precisely documented at all times and for all parties involved. "An important aspect for us is that by digitalising processes, we can flexibly integrate changes", says Terstegen. When modifications are made, the electrical designer sees online whether the component in question is already wired, and the change immediately appears on the tablet of the wiring technician. Conversely, the wiring technician may identify an error. The change is then transmitted to the electrical designer in real time.
Interface problems in switchgear engineering
One challenge in transmitting data across companies is the general absence of a standardised interface for the 3D model of a control cabinet. In other industries, such as the building sector, the IFC interface standardises the 3D representation of a building. With Eplan Pro Panel, Eplan gives the option of describing a control cabinet's digital twin in 3D. On the basis of this model, all information required in downstream processes can be provided via standardised interfaces. Customers and service providers can use the data from the digital twin in their own processes. No extra documents are required for the sharing of information.
Flexibility across company boundaries
Working with the digital twin means all those involved are always up to date. The digital twin leads to highly efficient cooperation across companies, between customers and cabinet manufacturers as well as between cabinet manufacturers and their suppliers. The customer also gains by having a good overview of the process and the project's progress. Even the smallest details can be viewed at an instant. This makes agreement easier because issues can be jointly viewed in the model and discussed.
About Unitechnik
Unitechnik Systems GmbH is based in Wiehl and has been one of the leading suppliers of industrial automation and information technology for four decades. The second generation of the family-owned company designs and implements tailor-made systems for internal logistics, cargo facilities and production. Unitechnik operates worldwide as a system integrator and full supplier. Professional project management and support of implemented plants are the basis of long-term business relations and ensure the security of customer investments. Unitechnik clients include well-known companies such as Claas, Dehn, Emirates, Linde, Lindt & Sprüngli, Nobilia, Otto Fuchs, Soennecken and Turck.
Author: Dirk Schütz, head of department and sales for control cabinet engineering at Unitechnik
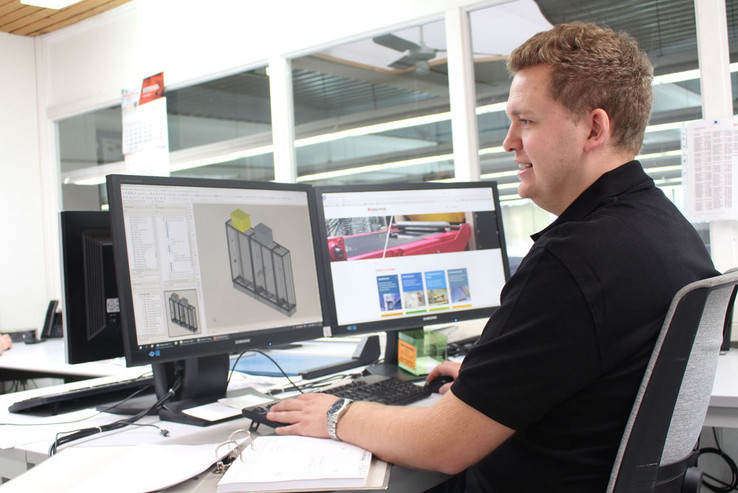
The digital twin accompanies the entire production process and reduces the likelihood of errors. It also plays an important role in functional checks.
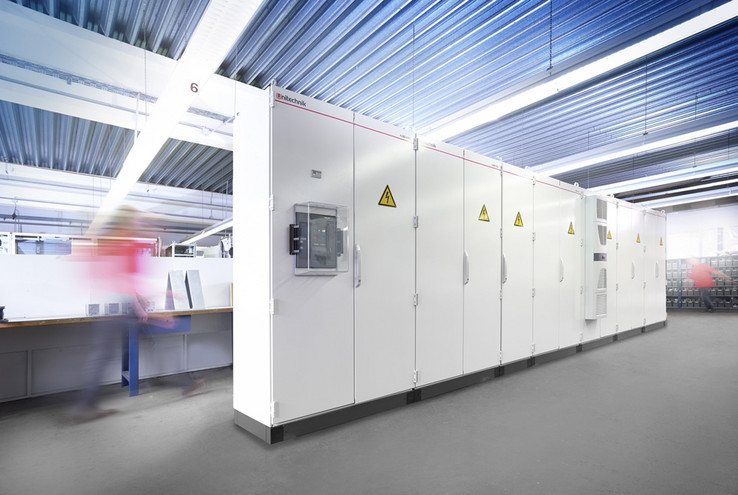
Fully digitalised process flows increase efficiency in production and planning by almost 40 percent. © Unitechnik Systems GmbH